This project embarks on a pioneering journey to explore and implement advanced technologies in the realm of electric vehicles (EVs), aiming to enhance their efficiency, performance, and sustainability. Assoc. Prof. Dr. Derya Ahmet Kocabaş from Istanbul Technical University, Department of Electrical Engineering and his research team will design and implement a highly efficient electric vehicle drive system. This is built on an integrated approach to enhance the total efficiency of all system components, from the battery to the wheel.
The project team members are listed below.
Assoc. Prof. Dr. S. Barış Öztürk (ITU, Dept. of Electrical Engineering)
Asst. Prof. Dr. Mehmet Onur Gülbahçe ((ITU, Dept. of Electrical Engineering)
Lect. Abdulsamed Lordoğlu (ITU Energy Institute)
Assoc. Prof. Dr. Ömer Cihan Kıvanç (Istanbul Okan Univ., Dept. of Electrical and Electronics Engineering
Asst. Prof. Dr. Emre Avcı (Duzce University, Dept. of Electrical and Electronics Engineering)
Assoc. Prof. Dr. Gamze Gediz İliş (Gebze Tech. Univ., Dept. of Mechanical Engineering)
Members supported by TUBITAK Scholarship
Res. Asst. Enis Barış Bulut (Edirne Univ., Ph.D. Candidate)
Res. Asst. Güven Onur (ITU, Ph.D. Candidate)
Res. Asst. Batı Eren Ergun (ITU, Ph.D. Candidate)
Mustafa M. Avcı (ASELSAN, Ph.D. Candidate)
Berk Hızarcı (ITU, M.Sc.)
One of the primary focuses is the integration of an 800V DC bus in passenger cars, a technology not currently utilized but holds promising potential for significant advancements in EV systems. The use of an 800 V DC bus is anticipated to reduce charging times and losses, leading to enhanced energy efficiency and extended vehicle range.

Fig. 1: Trade of diagram for a higher DC bus voltage value.
In tandem with the 800 V DC bus, the project also delves into the utilization of a three-phase 3-level multi-level inverter, another innovative technology not yet employed due to the current absence of the 800 V DC bus in EV infrastructure. The integration of these advanced technologies is anticipated to revolutionize the EV landscape, offering enhanced performance and efficiency by reducing the voltage stress on the semiconductor switching elements, leading to increased longevity and reliability of the EV systems.
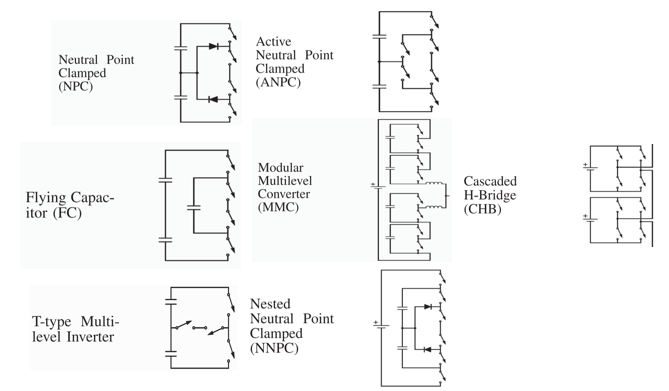
Fig. 2: Fundamental multi-level inverter topologies.
The project further explores the prospective integration of silicon carbide (SiC)-based wide-bandgap (WBG) power semiconductors in EV traction systems. As these advanced semiconductors gain traction, their incorporation into EV systems is expected to yield substantial benefits, including higher thermal conductivity and electrical efficiency, leading to improved performance and reduced energy losses in the traction systems.
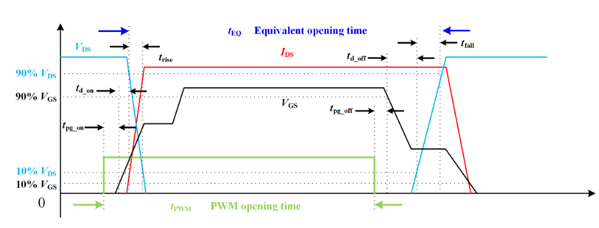
Fig. 3: General switching characteristics for a power-electronic switch.
The project will also employ Hardware-In-The-Loop (HIL) and Power-Hardware-In-The-Loop (P-HIL) simulations to further augment the efficiency of the EV traction system. These simulations will allow for real-time testing and adjustments, ensuring optimal performance, reliability, and sustainability by identifying and addressing issues promptly, leading to enhanced system efficiency and reliability.
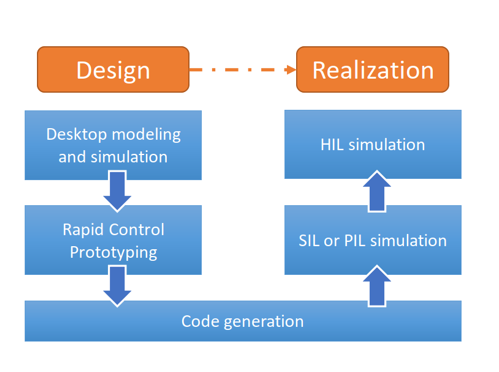
Fig. 4: V-diagram for model-based design.
A critical component of the project is the evaluation and selection of the most suitable motor for the proposed EV system. Four potential three-phase AC motors, namely the induction motor (IM), interior permanent magnet synchronous motor (IPMSM), synchronous reluctance motor (SynRM), and PM-assisted synchronous reluctance motor (PMa-SynRM), will be meticulously analyzed to ascertain the most compatible and efficient option for integration with the 800 V DC bus and three-phase 3-level multi-level inverter. A high-current density is chosen to provide higher power density values. Innovative cooling solutions will be added to the motors for safety.

In addition to these advancements, a vector control algorithm for the three-phase multi-level (3-level) inverter will be developed for the chosen motor within the project framework. This sophisticated control algorithm will be meticulously designed to optimize the performance and efficiency of the motor, ensuring seamless integration with the 800 V DC bus and 3-level multi-level inverter.

To ensure optimal operation and longevity, the project will implement liquid cooling for both the motor and the inverter, providing efficient thermal management and enhancing the overall performance and reliability of the EV system. The entire system will undergo rigorous testing on a test dynamometer system, ensuring its performance, efficiency, and reliability meet the highest standards of excellence. This comprehensive project, encompassing these innovative technologies and methodologies, stands as a beacon of advancement in electric vehicle technology, paving the path for a more efficient, sustainable, and high-performing future in electric mobility.
The study is supported within the scope of the TUBITAK Center of Excellence Support Program (1004) named as İLATERA: Environmentally Compatible Sustainable Advanced Vehicle Technologies Platform and is conducted by the ITU Advanced Vehicle Technologies Application and Research Center (ITU ILATAM). The total project duration is 24 months and the budget is approximately 7 million TL. The first quadrant of the project was recently completed and the primitive optimizable electric motor models providing 80 kW shaft power were designed. In the next quadrant, the optimized electric motor designs will be determined and the multi-level inverter design will be initiated.
